Discover What is Porosity in Welding and Its Result on Architectural Honesty
Wiki Article
Porosity in Welding: Identifying Common Issues and Implementing Ideal Practices for Avoidance
Porosity in welding is a pervasive problem that typically goes undetected until it creates considerable troubles with the integrity of welds. This common issue can compromise the toughness and resilience of bonded structures, posing safety and security dangers and bring about pricey rework. By comprehending the origin of porosity and executing efficient prevention methods, welders can substantially enhance the high quality and dependability of their welds. In this discussion, we will explore the vital factors contributing to porosity formation, analyze its destructive results on weld efficiency, and review the most effective methods that can be adopted to decrease porosity event in welding procedures.Usual Reasons of Porosity
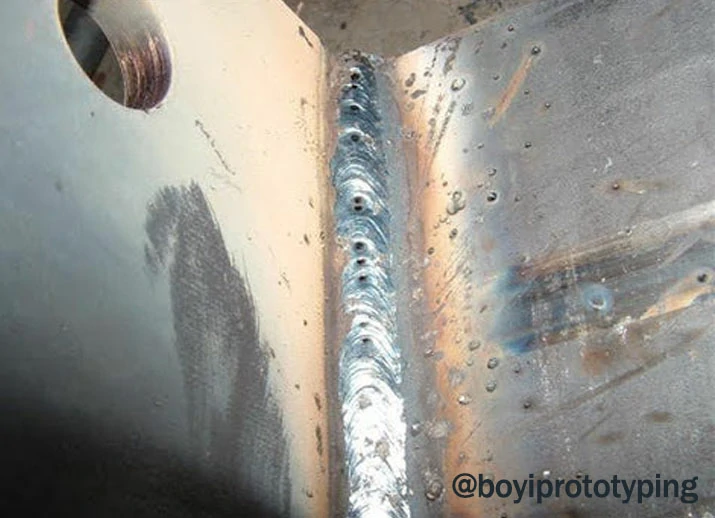
Another frequent wrongdoer behind porosity is the visibility of contaminants externally of the base steel, such as oil, oil, or rust. When these pollutants are not properly removed before welding, they can vaporize and end up being caught in the weld, creating defects. In addition, making use of filthy or wet filler products can present impurities into the weld, adding to porosity concerns. To minimize these common sources of porosity, complete cleaning of base metals, appropriate shielding gas choice, and adherence to optimum welding specifications are essential techniques in accomplishing high-grade, porosity-free welds.
Impact of Porosity on Weld Top Quality

The existence of porosity in welding can dramatically compromise the structural stability and mechanical residential or commercial properties of bonded joints. Porosity develops gaps within the weld metal, damaging its total strength and load-bearing capacity.
Welds with high porosity levels often tend to display reduced effect strength and lowered capability to flaw plastically before fracturing. Porosity can hamper the weld's capability to effectively transfer forces, leading to early weld failing and potential security dangers in crucial structures.
Best Practices for Porosity Prevention
To improve the structural integrity and quality of bonded joints, what particular actions can be carried out to reduce the occurrence of porosity during the welding procedure? Utilizing the right welding method for the particular material being welded, such as readjusting the welding angle and weapon placement, can additionally avoid porosity. Regular assessment of welds and prompt removal of any type of concerns recognized throughout the welding process are important practices to prevent porosity and produce high-quality welds.Importance of Correct Welding Methods
Implementing proper welding strategies is paramount in making certain the architectural integrity and quality of bonded joints, building on the structure of reliable porosity prevention steps. Welding techniques directly impact the total stamina and durability of the welded framework. One essential facet of correct welding techniques is preserving the correct heat input. Extreme warmth can lead to raised porosity as a result of the entrapment of gases in the weld pool. Conversely, not enough heat may result in insufficient fusion, creating potential powerlessness in the joint. Additionally, making use of the appropriate welding specifications, such as voltage, present, and travel speed, is crucial for achieving audio welds with marginal porosity.weblink In addition, the selection of welding process, whether it be MIG, TIG, or stick welding, ought to straighten with the particular demands of the project to guarantee optimum results. Correct cleaning and preparation of the base steel, in addition to picking the appropriate filler material, are additionally important components of proficient welding strategies. By adhering to these finest practices, welders can reduce the risk of porosity development and create high-grade, structurally audio welds.

Testing and Quality Assurance Procedures
Quality control measures play a vital function in confirming the honesty and dependability of welded joints. Testing treatments are necessary to find and protect against porosity in welding, making sure the toughness navigate to these guys and resilience of the last product. Non-destructive screening approaches such as ultrasonic screening, radiographic screening, and visual assessment are typically used to recognize possible problems like porosity. These methods permit for the assessment of weld quality without jeopardizing the integrity of the joint. What is Porosity.Post-weld inspections, on the other hand, examine the last weld for any why not try these out flaws, consisting of porosity, and validate that it fulfills defined standards. Applying a comprehensive top quality control plan that includes complete screening treatments and evaluations is vital to reducing porosity concerns and making certain the total quality of bonded joints.
Conclusion
Finally, porosity in welding can be an usual problem that affects the top quality of welds. By recognizing the common reasons for porosity and applying ideal methods for avoidance, such as proper welding techniques and screening steps, welders can make sure top quality and dependable welds. It is important to focus on avoidance techniques to minimize the event of porosity and maintain the stability of bonded structures.Report this wiki page